Multi-angle analysis of the correct use of laser cutting machine cutting metal materials
To ensure that the laser cutting machine can be stable, high-quality cutting of metal materials, you need to consider from the parameters of the equipment, material characteristics, operating procedures and other aspects. The following for you to elaborate the relevant content.
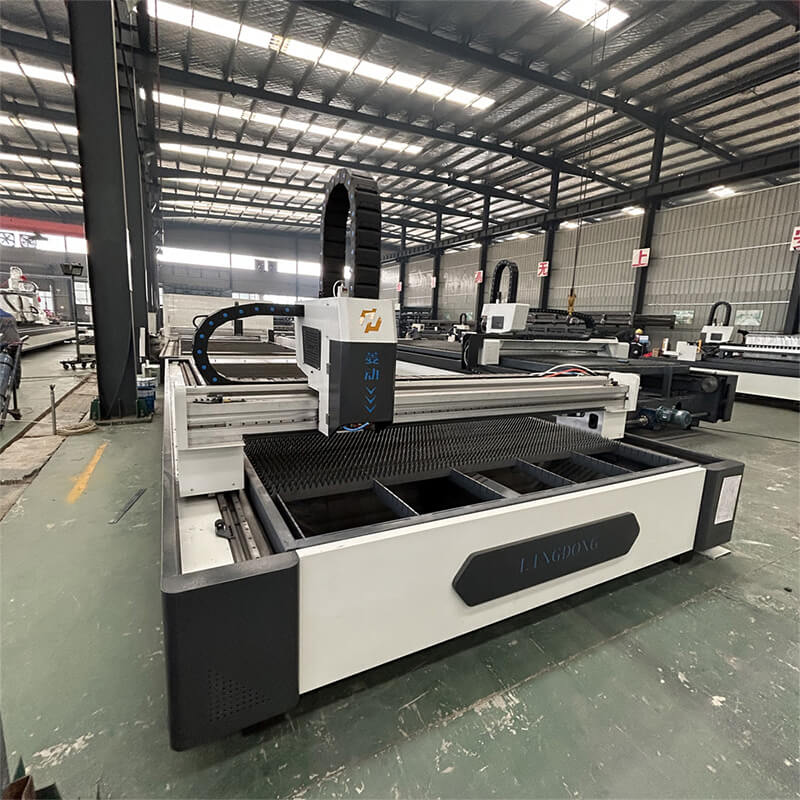
I. Equipment parameter setting
Power adjustment: according to the thickness and material of the metal material, precisely adjust the laser power. For example, cutting thicker stainless steel plate, need higher power to ensure that enough energy to penetrate the material; while cutting thin plate, too high power is easy to cause the plate to burn through.
Cutting speed: cutting speed and power need to match. Too fast, it may lead to incomplete cutting; too slow, it will make the kerf wider, the heat-affected area increases, affecting the cutting quality.
Focus position: the focus position determines the distribution of laser energy on the material surface. For different thicknesses of metal, the focus position should be adjusted so that the laser energy is concentrated in the appropriate cutting depth to obtain the best cutting results.
Second, the material characteristics to consider
Material differences: different metal materials have different absorption rates of laser. Like aluminium alloy, its absorption rate of the laser is low, cutting requires higher power and suitable auxiliary gas to improve the cutting quality; while carbon steel on the laser absorption rate is relatively high, cutting process is relatively easy.
Material surface condition: The flatness and roughness of the surface of the material, as well as whether there is a coating, etc., will affect the cutting effect. Uneven surface or impurities may lead to unstable cutting process or even damage the lens.
Third, the operation process specification
Switch on and warm up: Before formal cutting, let the equipment warm up, so that the laser and other key components reach a stable working condition to ensure the stability and precision of cutting.
Workpiece fixing: Make sure the metal material is fixed firmly on the working table to avoid displacement during the cutting process, which will affect the cutting precision and quality.
Use of auxiliary gases: choose the appropriate auxiliary gas according to the material and cutting requirements, such as oxygen is commonly used in carbon steel cutting, which can improve the cutting speed and quality of the kerf; nitrogen is suitable for stainless steel and other materials, which can prevent the kerf from oxidation.
Fourth, equipment maintenance and safety
Equipment maintenance: regularly check the laser cutting machine optical system, cooling system, transmission system, etc., to ensure the normal operation of the equipment. Timely replacement of worn parts, such as lenses, nozzles, etc., to ensure cutting quality.
Safety protection: the operator must wear protective glasses to prevent laser damage to the eyes; at the same time, pay attention to the safety warning signs around the equipment to avoid unrelated personnel close.