Laser welding in aluminium alloy material have what characteristics and advantages
Laser welding is a new type of welding, mainly used for welding thin-walled materials, precision parts, can achieve spot welding, butt welding, sealing welding, etc., high aspect ratio, small weld width, small heat-affected zone, welding speed, weld smooth, no need to deal with the welding or processing after welding is simple, high quality of weld, no air holes, precise control, small focal point, high positioning accuracy, easy to automate.
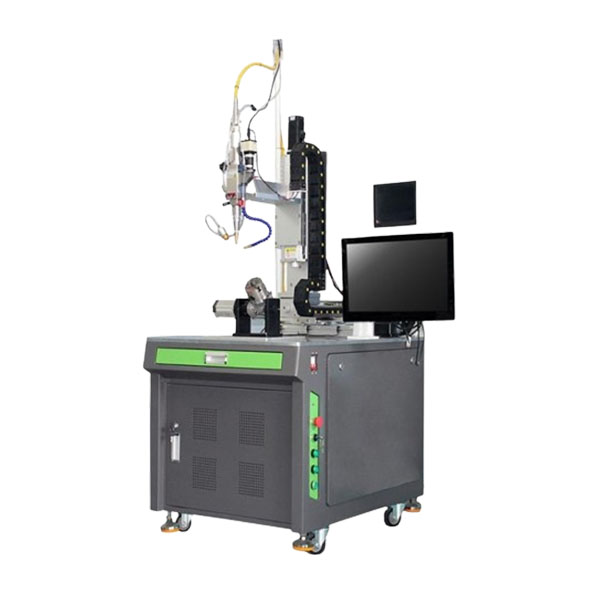
The common use of aluminium alloy also promotes the development of continuous welding technology of aluminium alloy, and has entered the aluminium application market. The conventional welding process for aluminium alloys presents many difficulties. For example, aluminium alloys have a very large thermal conductivity, about 2-4 times that of steel, and very poor heat resistance. Typically, aluminium alloys are not resistant to high temperatures and have a high coefficient of expansion, which makes them easy to produce. Welding distortion and the tendency to weld cracks are also evident. Due to these welding difficulties, fabricators have trouble finding better welding methods.
These seemingly insignificant leaks often bring unexpected trouble. The welding technology of continuous laser welding machine can easily solve these small leaks, thus effectively ensuring the integrity of the workpiece will not be damaged. So how does a continuous laser welder surpass traditional welding? Does it have better advantages?
Three unique advantages of laser welding aluminium alloys:
1, the laser beam has high energy density, high welding speed, no effect or slight effect on non-welded parts, font no thermal deformation;
2, high efficiency, no tool wear and tear, save consumables, speed is 8-10 times the traditional welding letter, can work for a long time, low heat;
3、Small size, easy to operate, high efficiency, strong and beautiful welding joints.