How to adjust the parameters of the laser marking machine to enhance the marking depth
In life, we will find that there are more and more products that need to be used for laser marking standard LOGO, pattern, date, two-dimensional code, barcode and so on. In the marking process will encounter marking marking depth is too shallow, the marking effect is not obvious, how should this be handled? We can explore the marking depth by adjusting the parameters from the following aspects. The parameter adjustment of the laser marking machine is crucial for obtaining high-quality marking results. The following are some suggestions compiled from empirical results:
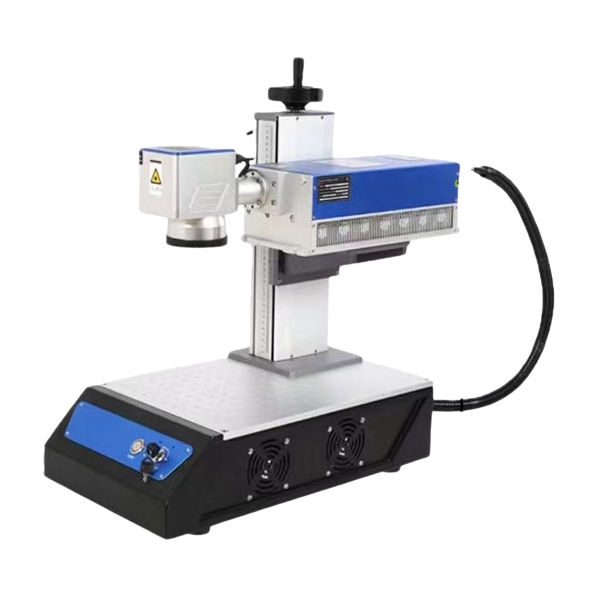
- Adjust the laser power
Laser power: Laser power is one of the key parameters affecting marking depth. Typically, increasing the laser power increases the depth of the marking. However, it is important to note that too much power may result in burning or damage to the material. Therefore, when adjusting the power, you need to balance the depth and the need to protect the material according to different material types and thicknesses. - Adjusting Marking Speed
Marking Speed: Marking speed also has an effect on depth. Lower speeds usually result in deeper marking because the laser has more time to interact with the material. However, speeds that are too slow can result in long marking times. Therefore, when adjusting the speed, a balance between productivity and marking quality needs to be considered. - Adjusting Marking Frequency
Marking Frequency: Marking frequency can also affect marking depth. A higher frequency usually results in a shallower marking effect, while a lower frequency results in a deeper marking effect. - Calibrate Focal Length
Focal length: The focal length of a laser marker is an important parameter that affects depth. Correct calibration of the focal length ensures that the laser is focused on the material surface with optimum shape and intensity. If the focal length is incorrect, the laser may not achieve the desired depth effect. - Reference Sample
Reference Sample: When adjusting the parameters of the laser marker, a reference sample can be made for testing and adjustment. Select materials similar to the actual application and mark them according to different combinations of parameters. By comparing the marking effect under different parameters, determine the most suitable parameter combination.
The above method requires comprehensive consideration of several factors, combined with sample testing and comparison, to find the best combination of parameters to meet different materials and marking needs. When adjusting the parameters, it is very important to pay attention to protect the material from damage and improve production efficiency.